Apollo Longboards
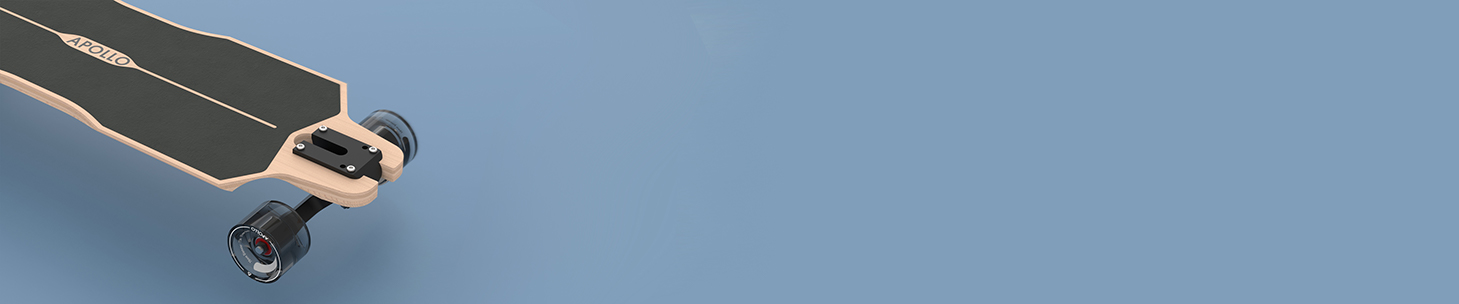
Conception
The first experience I had with longboards was while freshman me was studying in university. I was too strapped for cash at the time to buy a complete board. So I bought the wheels individually and made my own deck. I found out pine, aside from looking okay, was quite possibly the worst material to make a board from. Plywoods generally dominate when it comes to longboard deck materials, leaving hardwoods to historic designs, and softwoods entirely out of the design loop.
Getting a stern lecture on using university tools for university purposes didn't stop me. I went ahead and made a second board, this time out of a birch plywood cabinet side. However, the idea of a non plywood board still intrigued me. Perhaps there was a way to make it work?
Fast forward a couple years, and this idea of making longboards, especially out of things other than plywood, has become a senior project. The ideas I wanted to instill in the board was primarily the novelty of a new design at an affordable price.
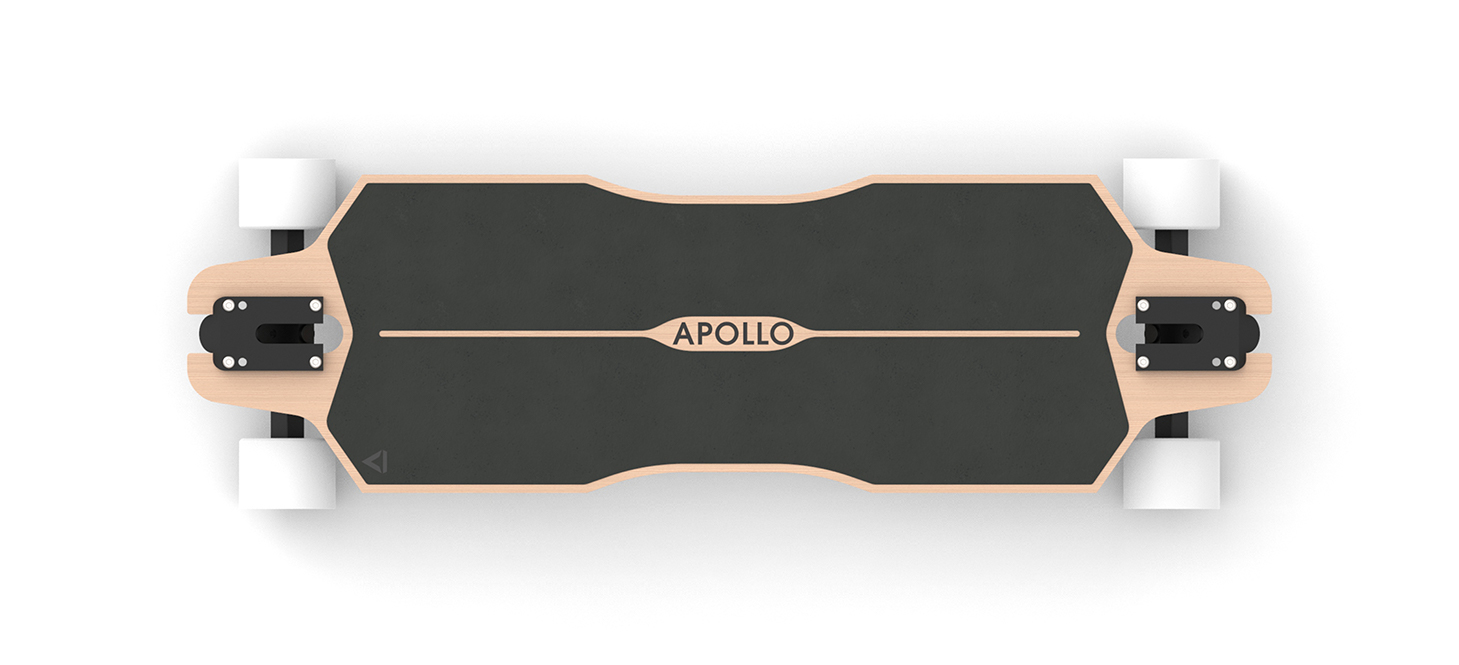
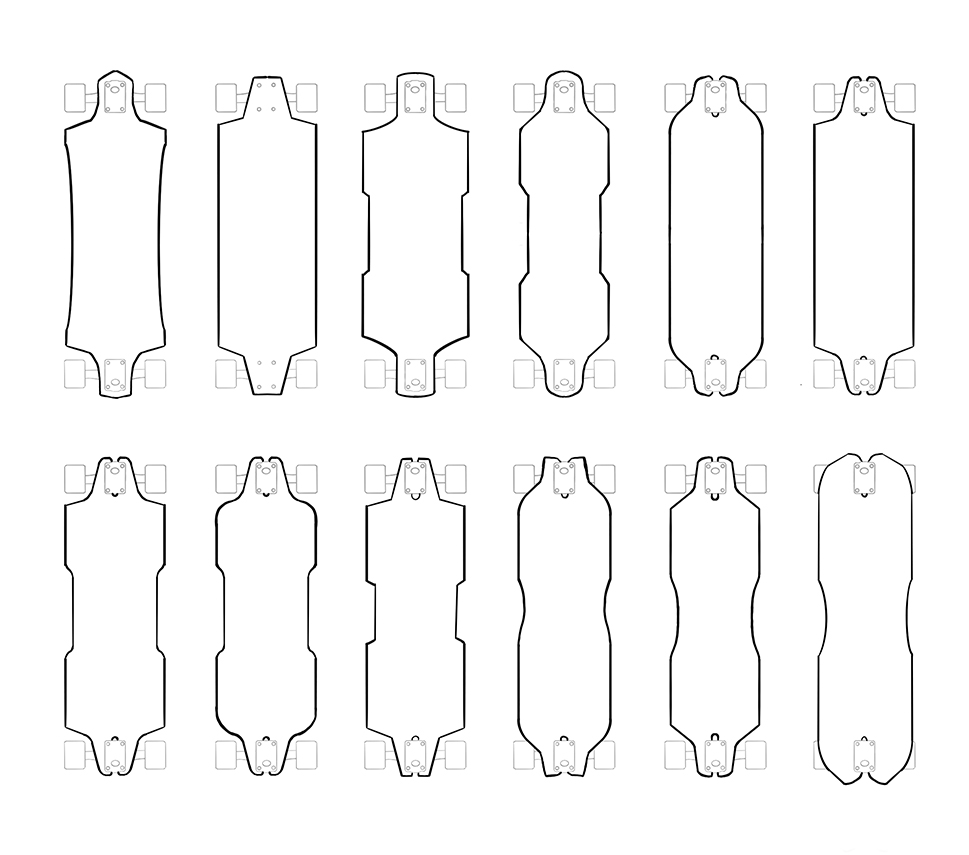
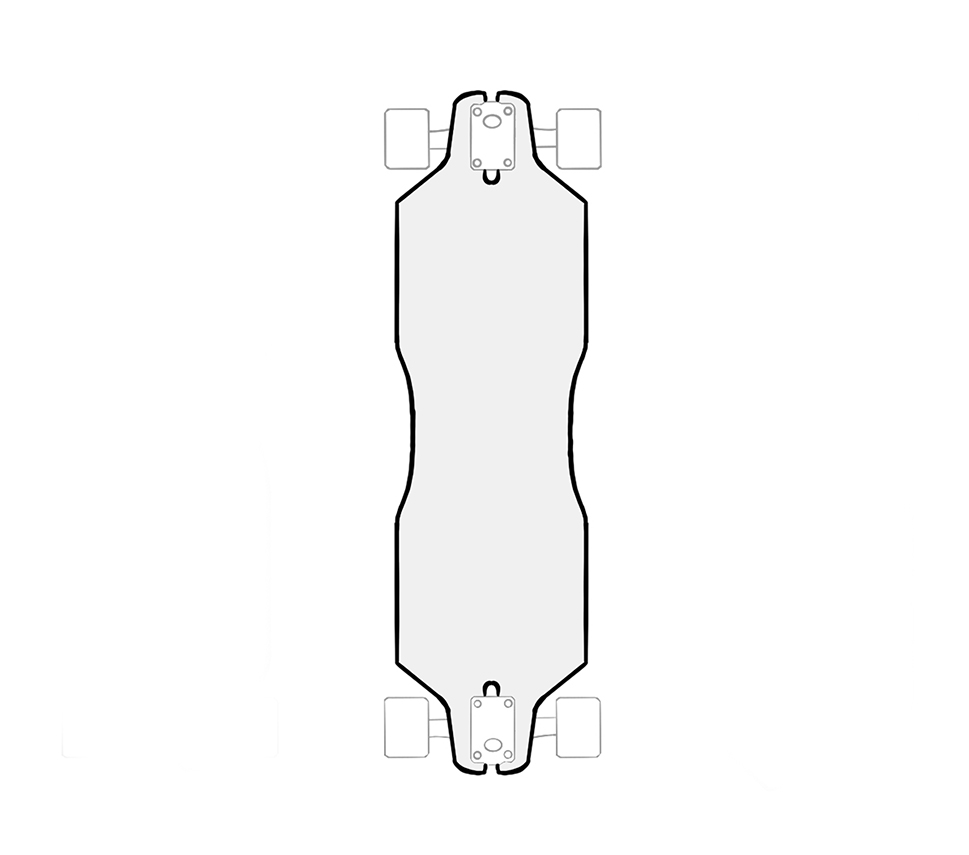
Board One - The Classic
There are many types of longboards, each with their own advantages and disadvantages. This first board is a balance between both extremes, which are agility and stability. The design is heavily influenced by a board that was made early in Marcus' college career. This is a refined version that builds on the very original design.
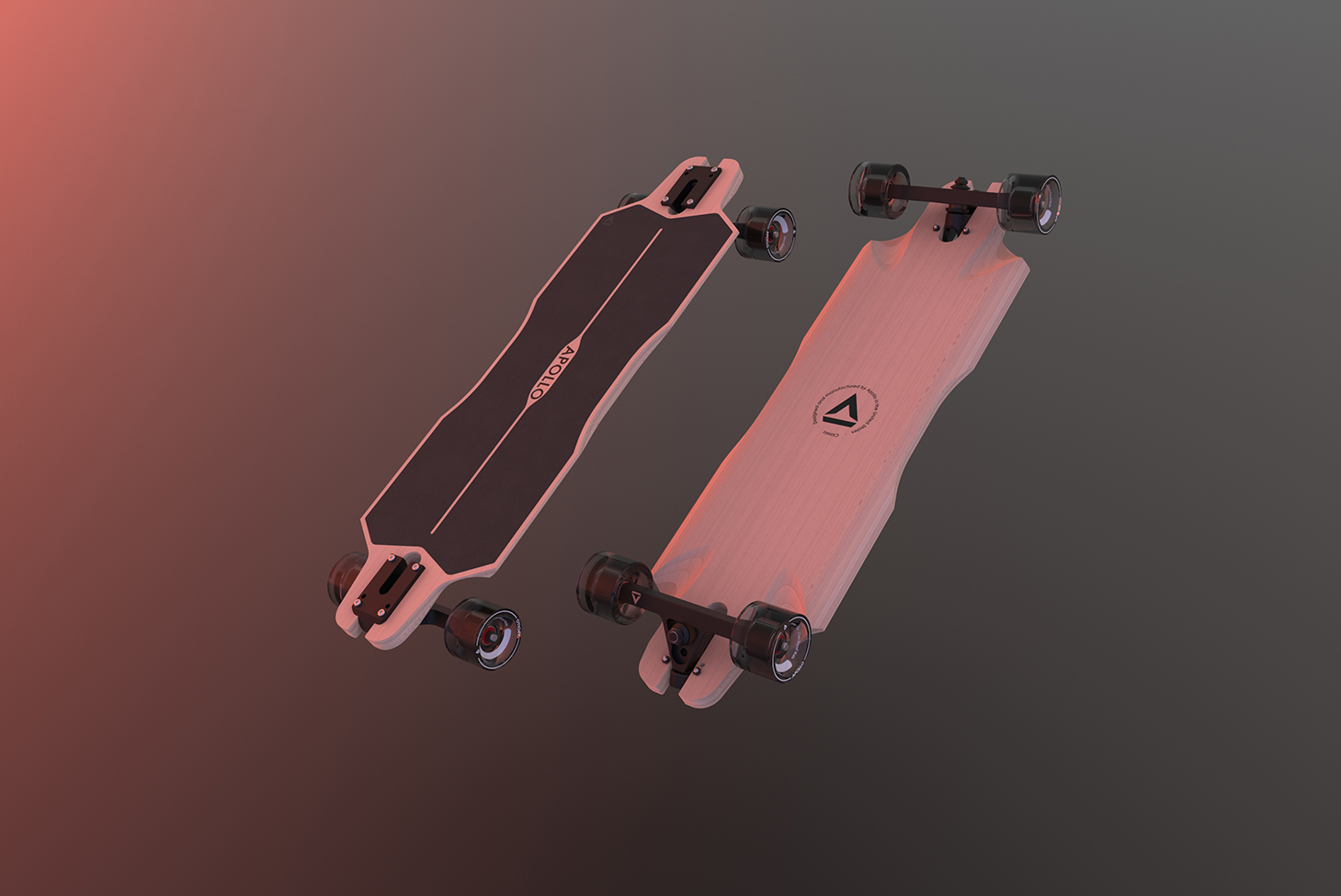
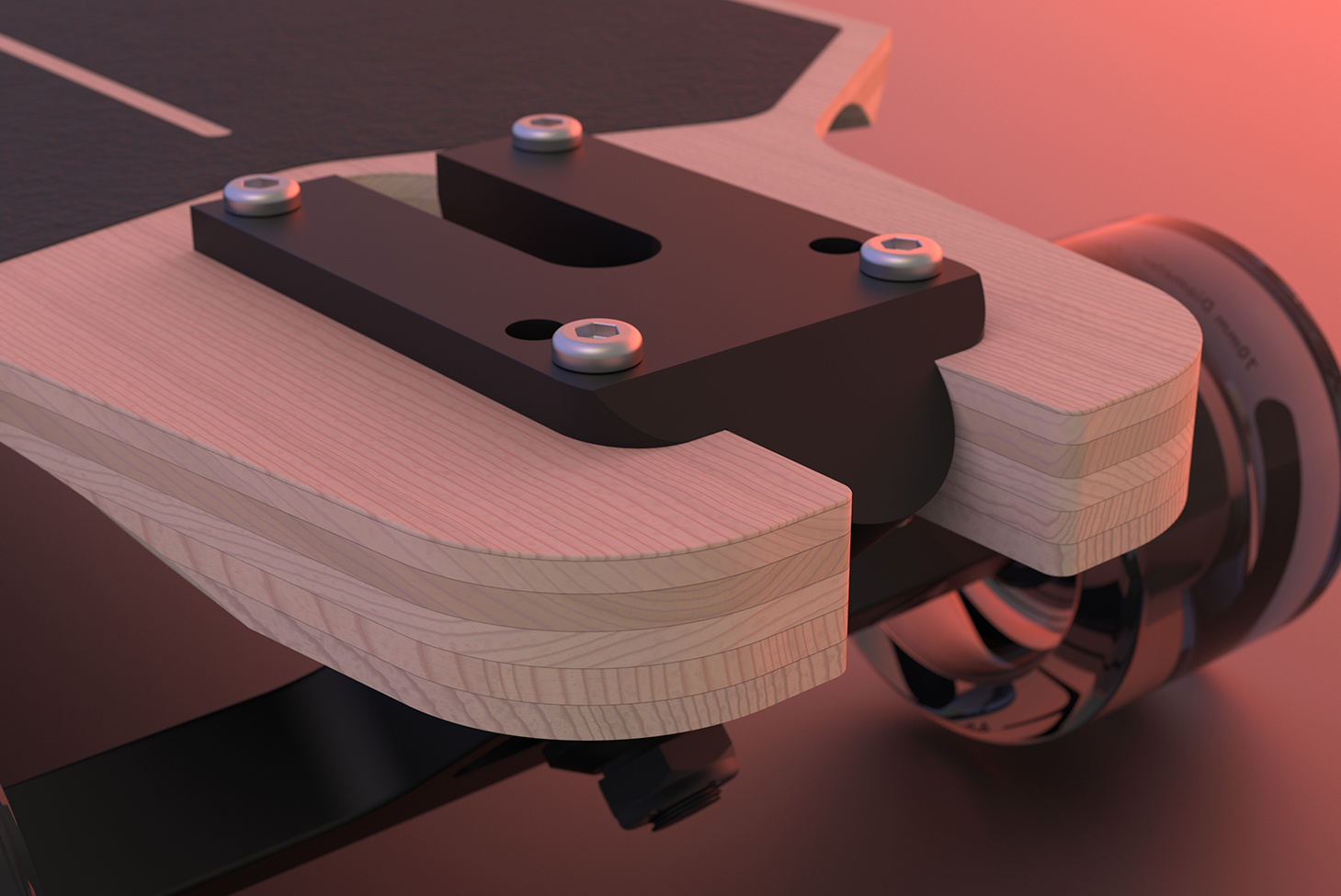
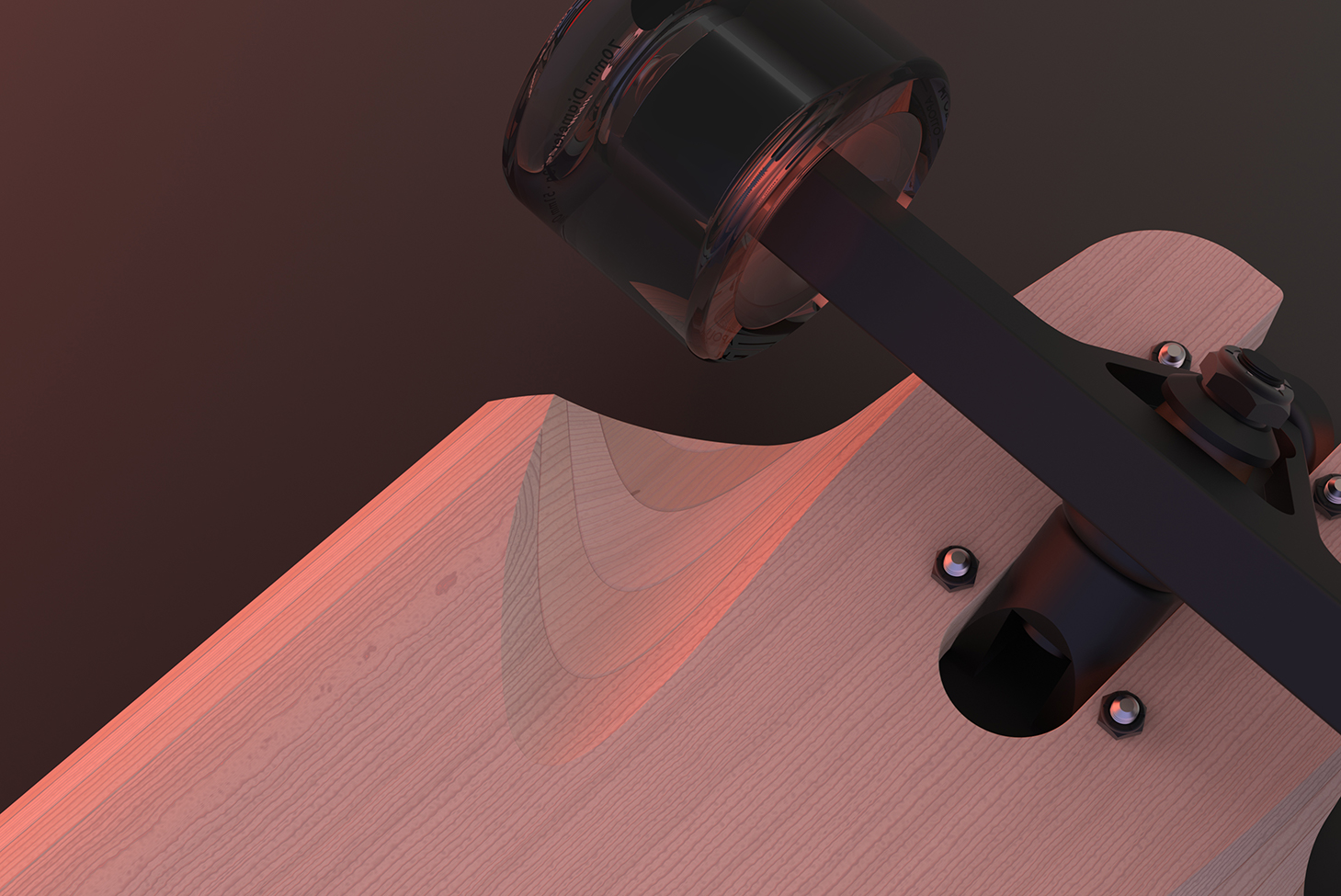
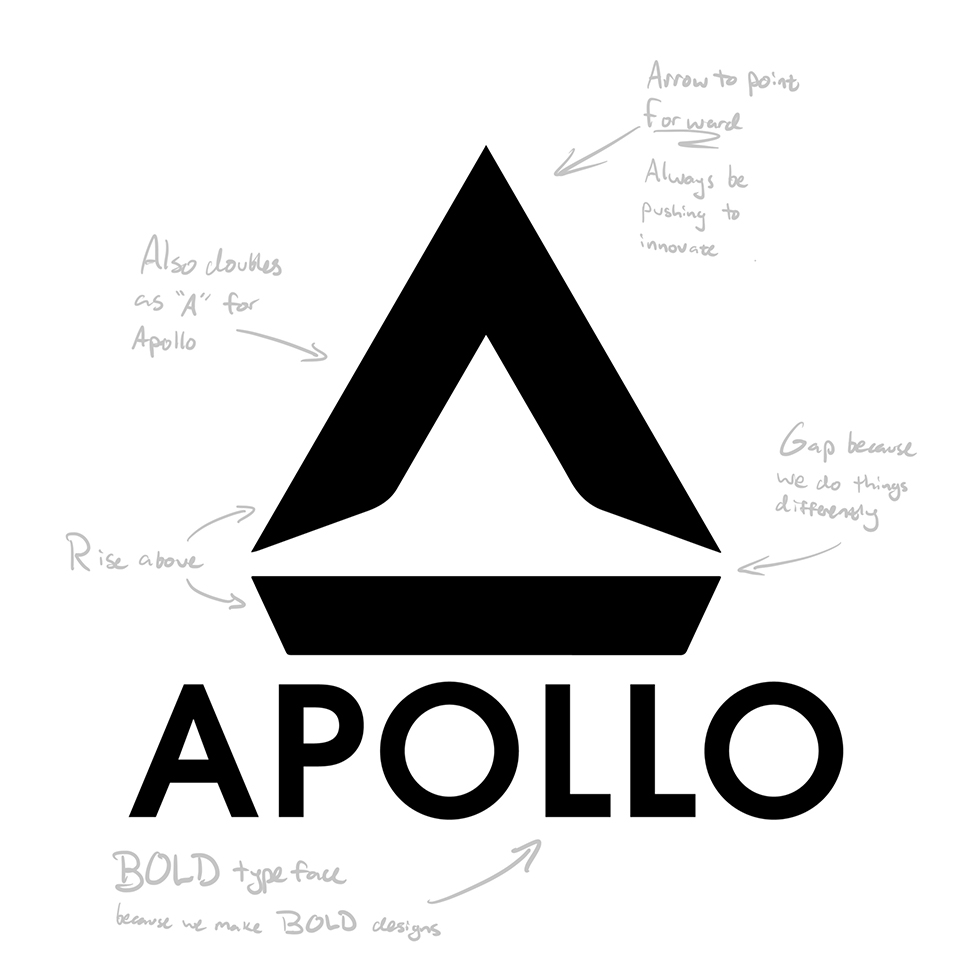
Brand Language
The logo of any brand should be a point of recognition for customers and establish a first impression. The logo design for Apollo stemmed from the idea of reaching for something better. The logo represents an "A" for Apollo, but also represents a mountain peak as the pinnacle of what we are trying to achieve. We believe in quality over quantity in every regard.
Everything Apollo should push the envelope in what is possible with both function and design. One example of this is the utilization of 3D printing throughout elements of the designs and aesthetics.
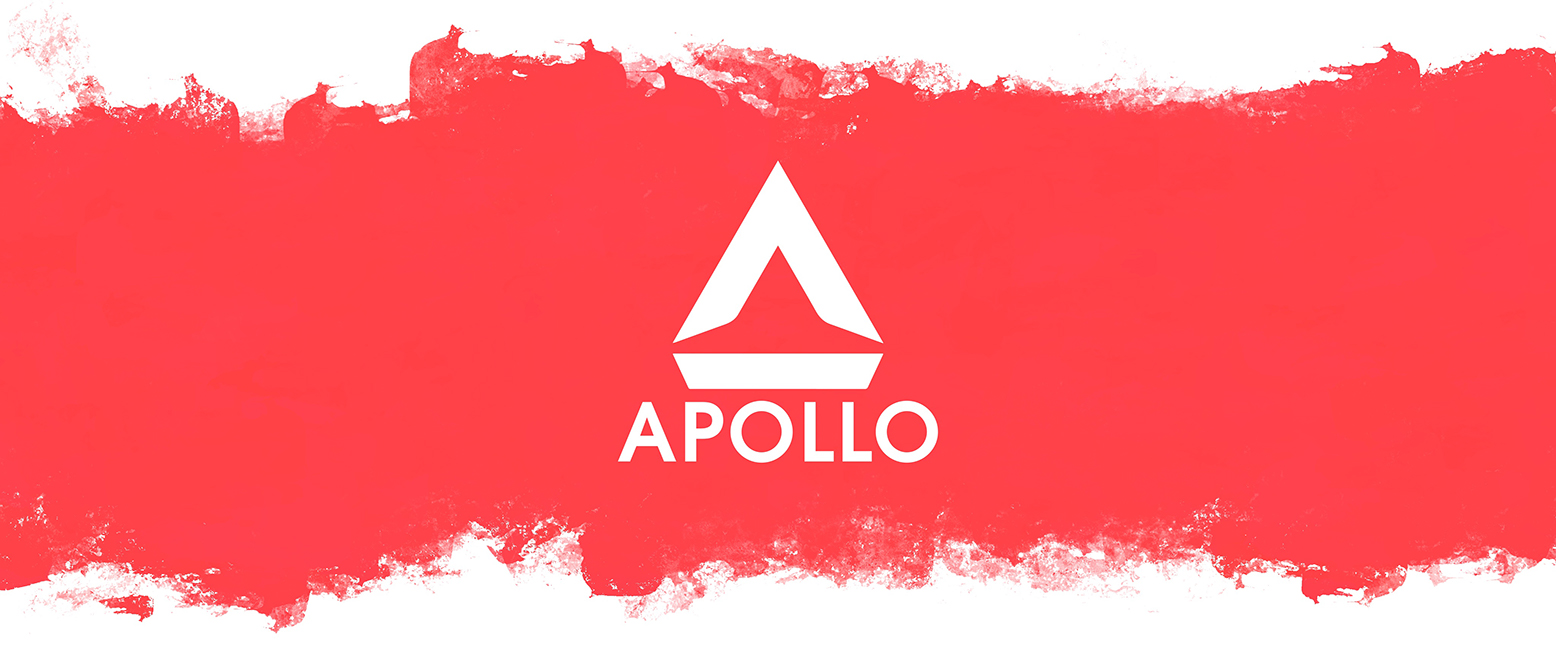
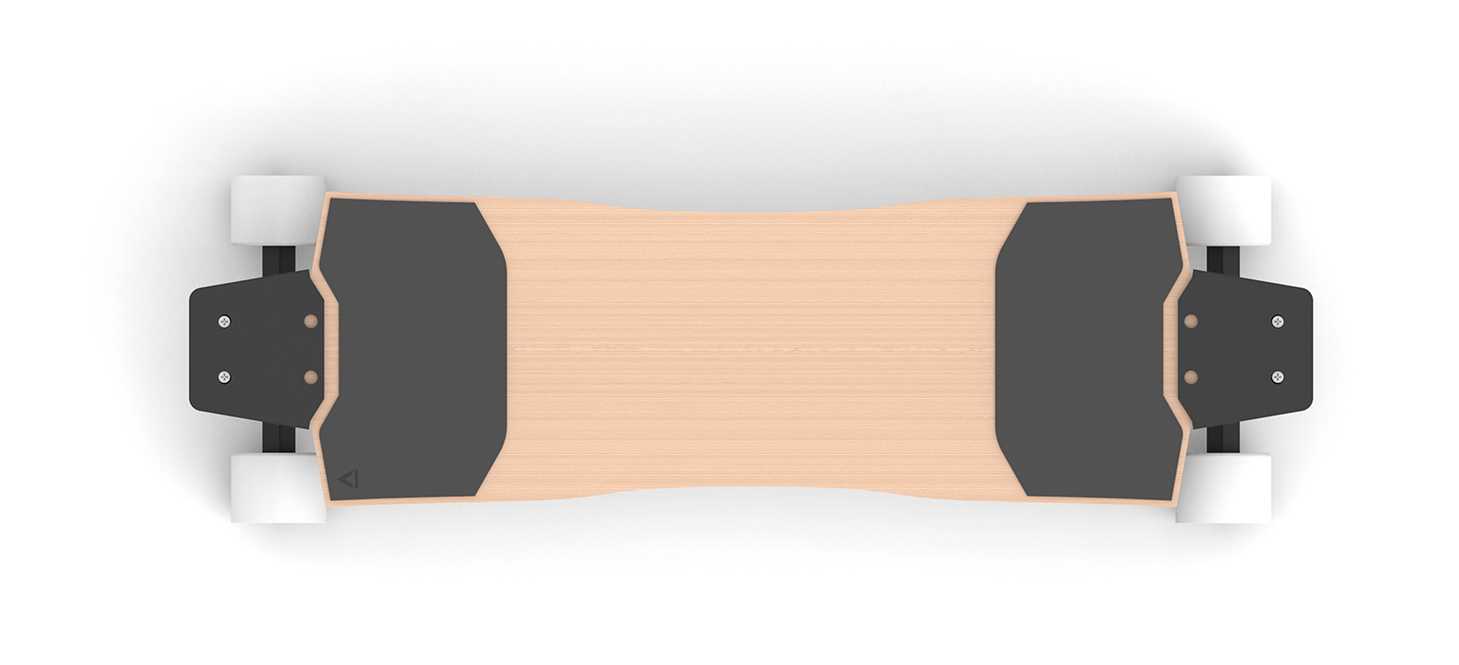
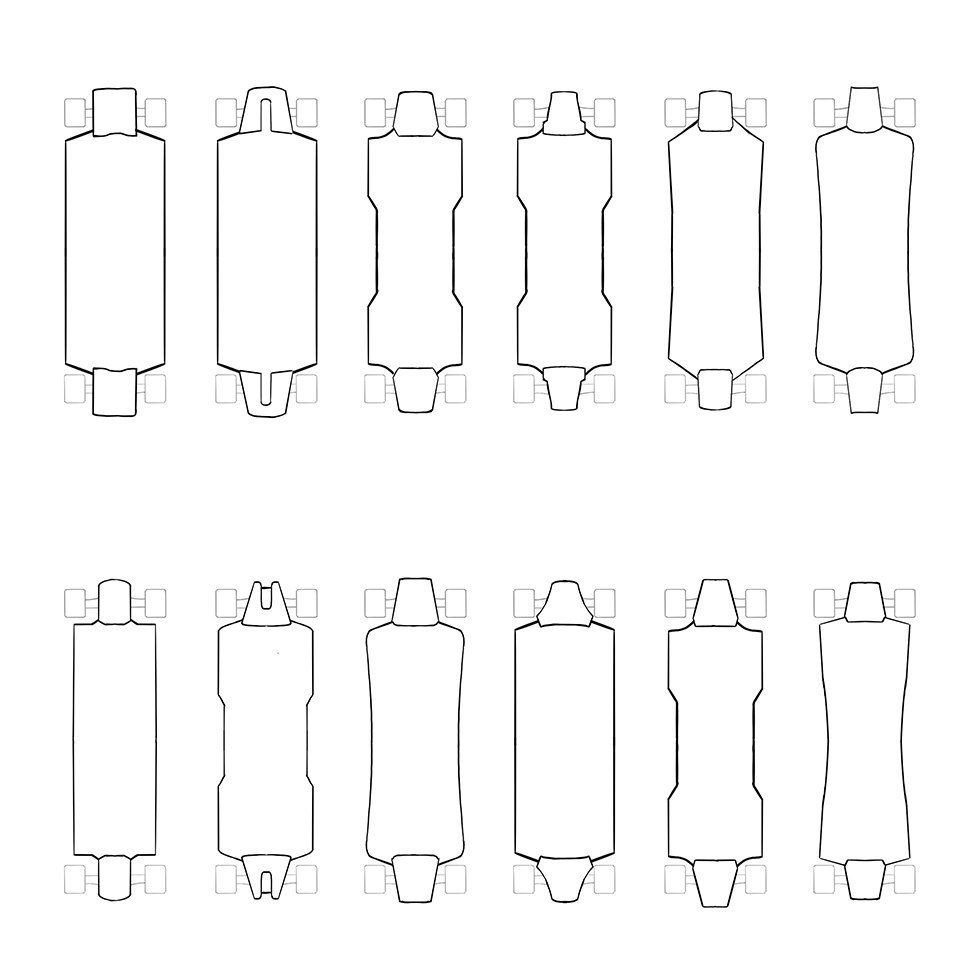
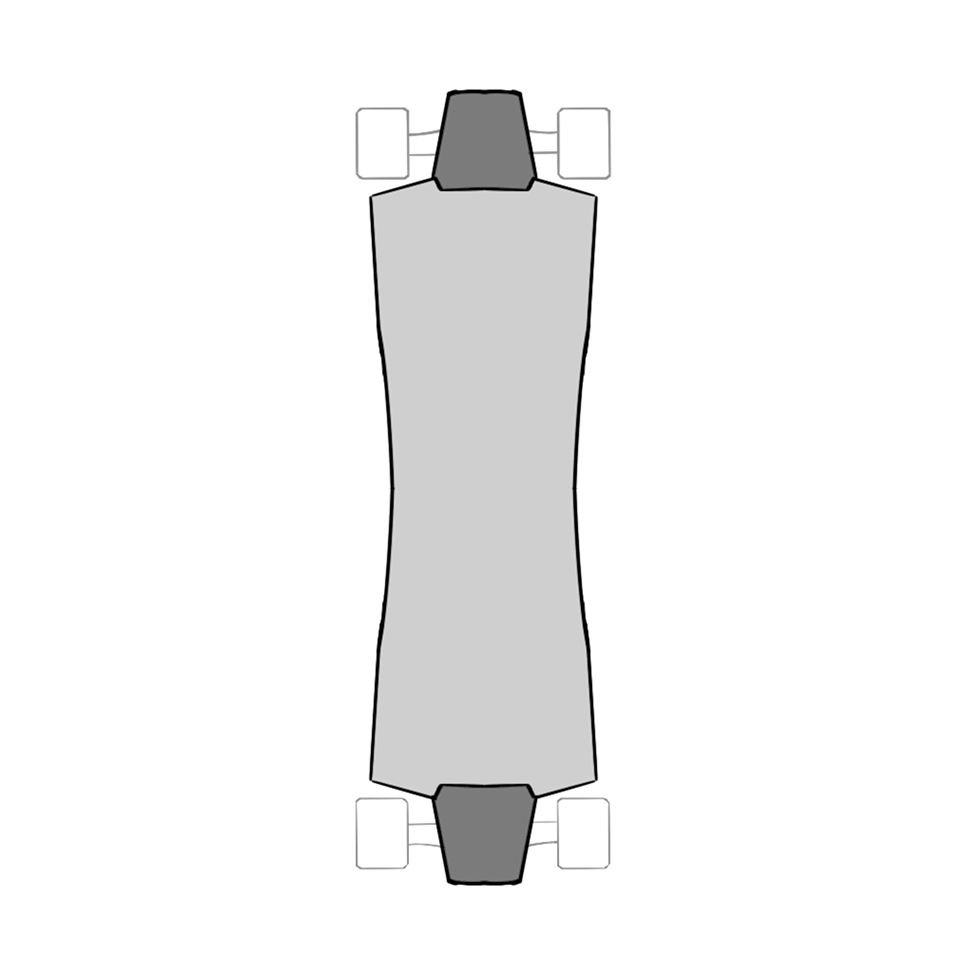
Board Two - Coreboard
One of the most popular materials for longboards is laminated plywood. This is because if you drill holes in solid wood, it often times will split very easily. This board is an attempt to solve this problem with using solid wood.
The solution is to not place the wheel mountings and bolts into the wood, rather use an endcap that clamps onto the board. This reduces the stress on the wood and prevents splitting. The endcap design incorperates 3D printing, making a part that would not be possible otherwise.
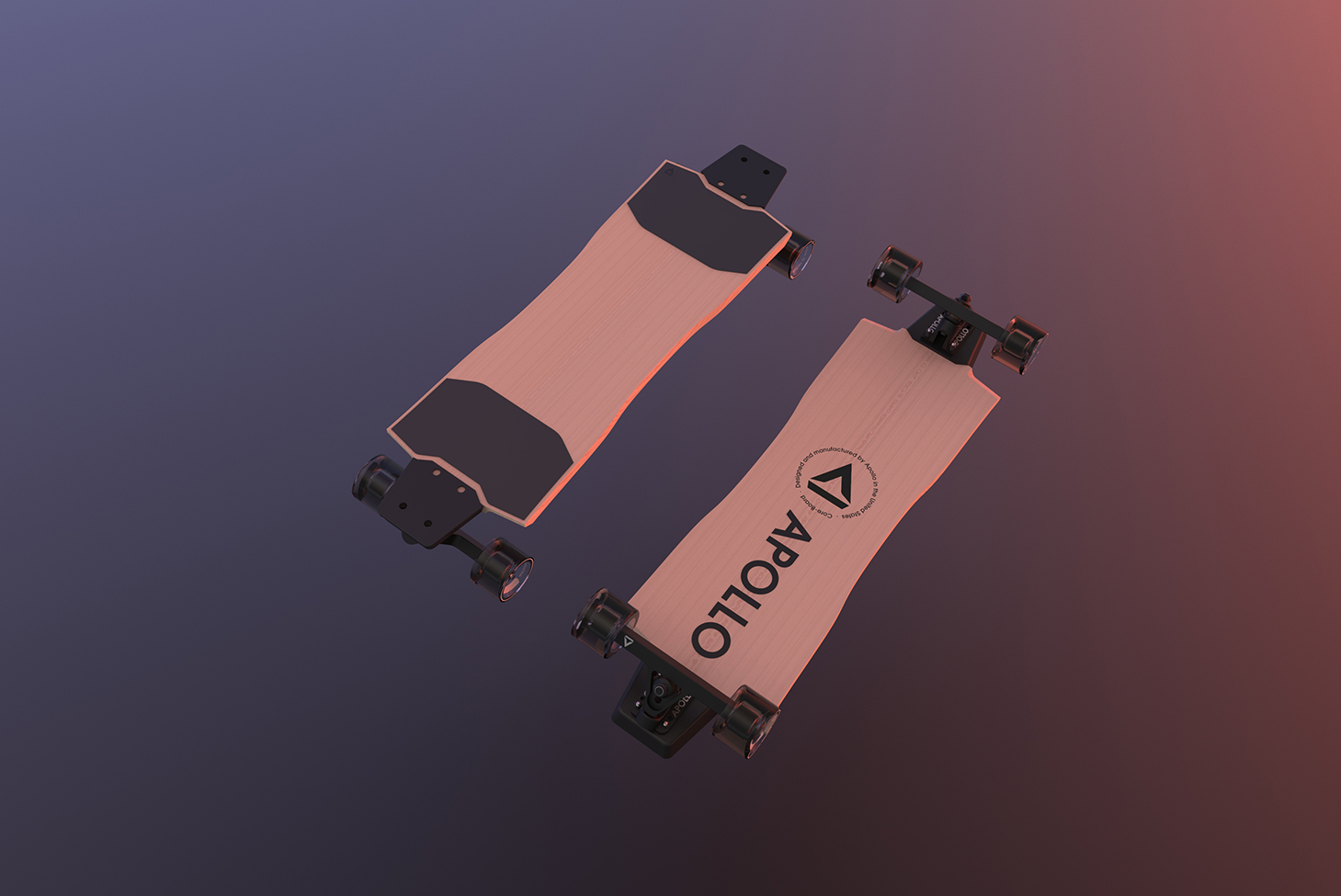
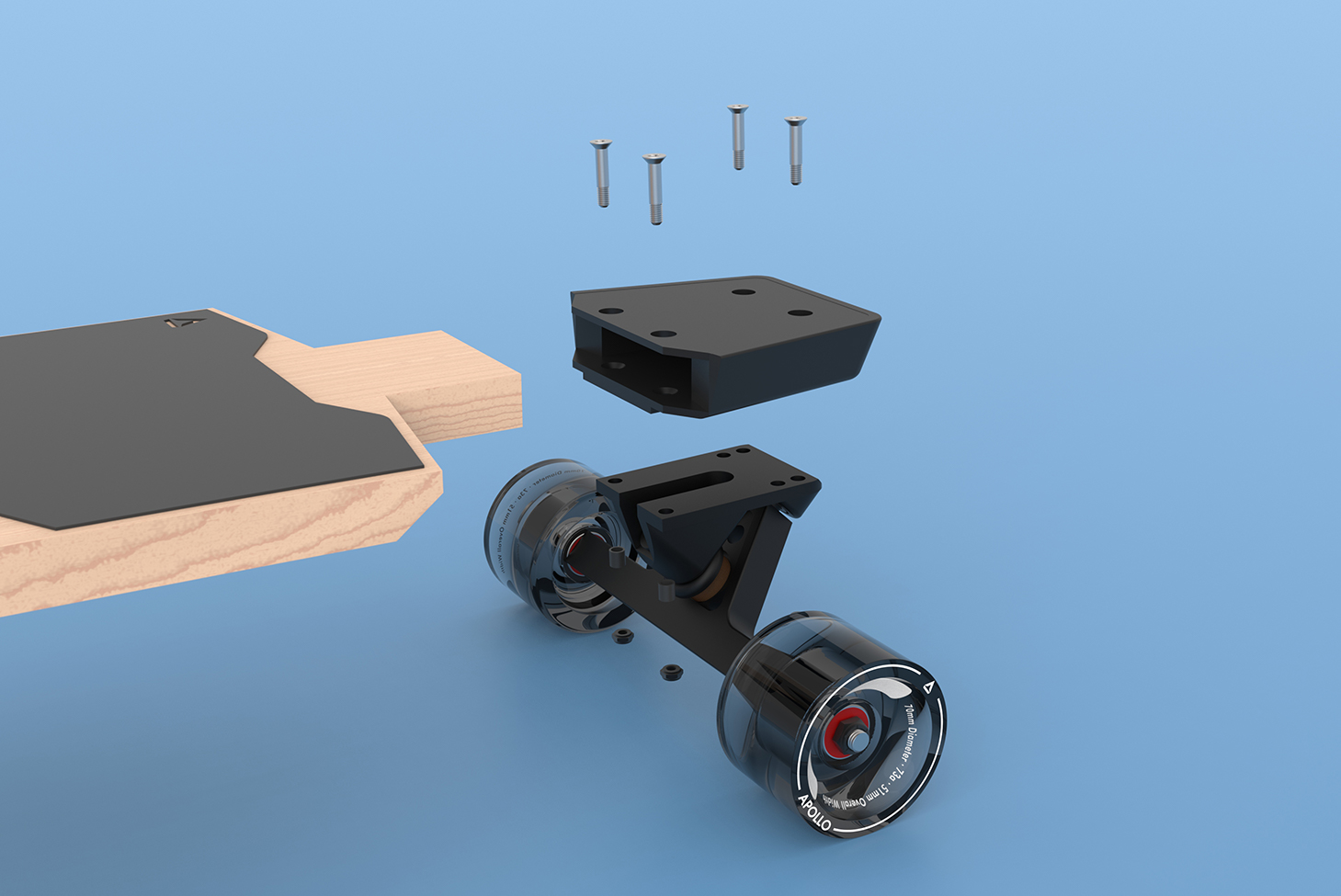
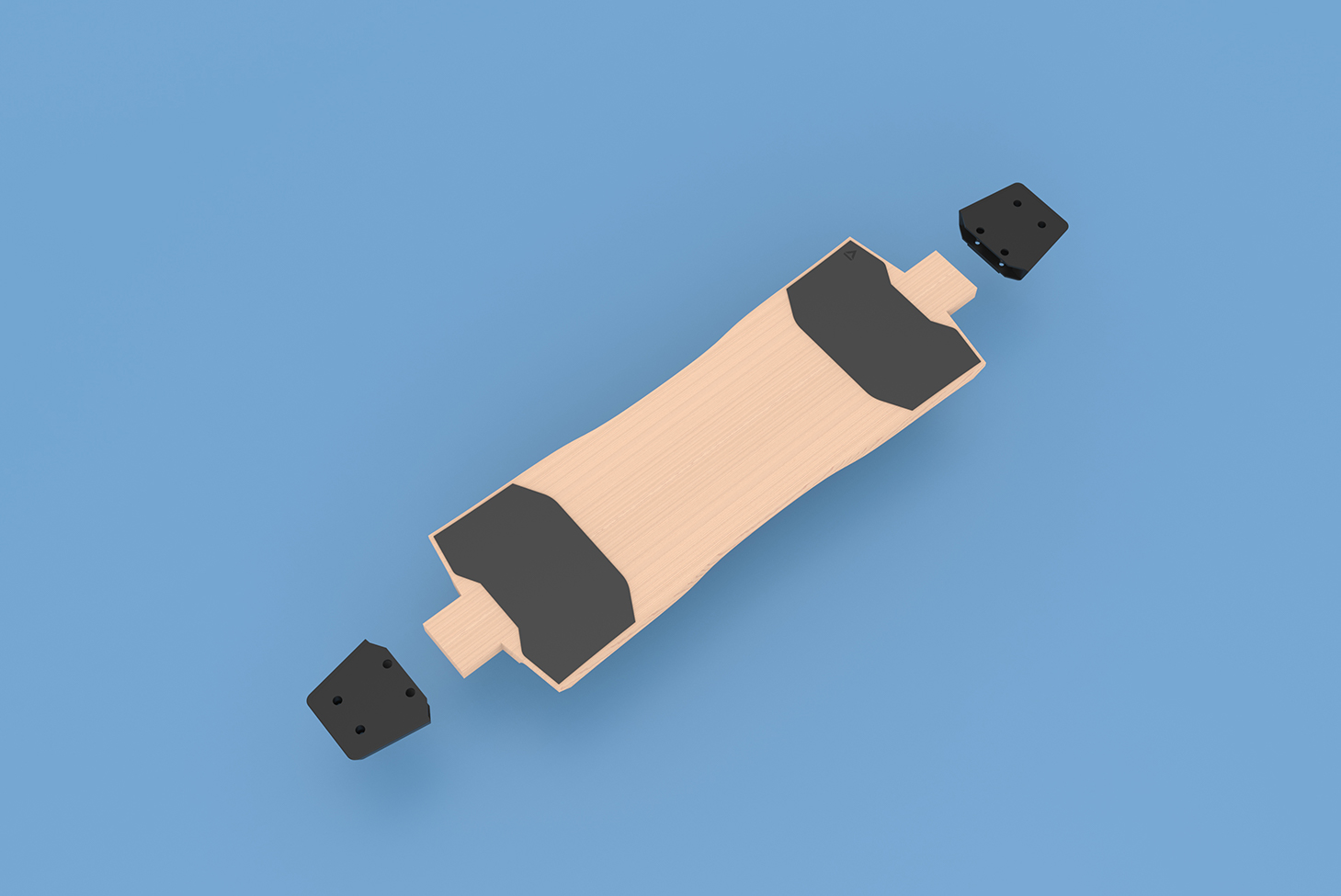
Flexibility
Something that is important to every longboard is the amount of flex the deck has. This heavily impacts ride dynamics and determines what role the board can fulfill. A more flexible deck will be better suited for cruising, and a stiffer deck will be more stable at high speed. With this being the case, different thicknesses can be chosen with each board.
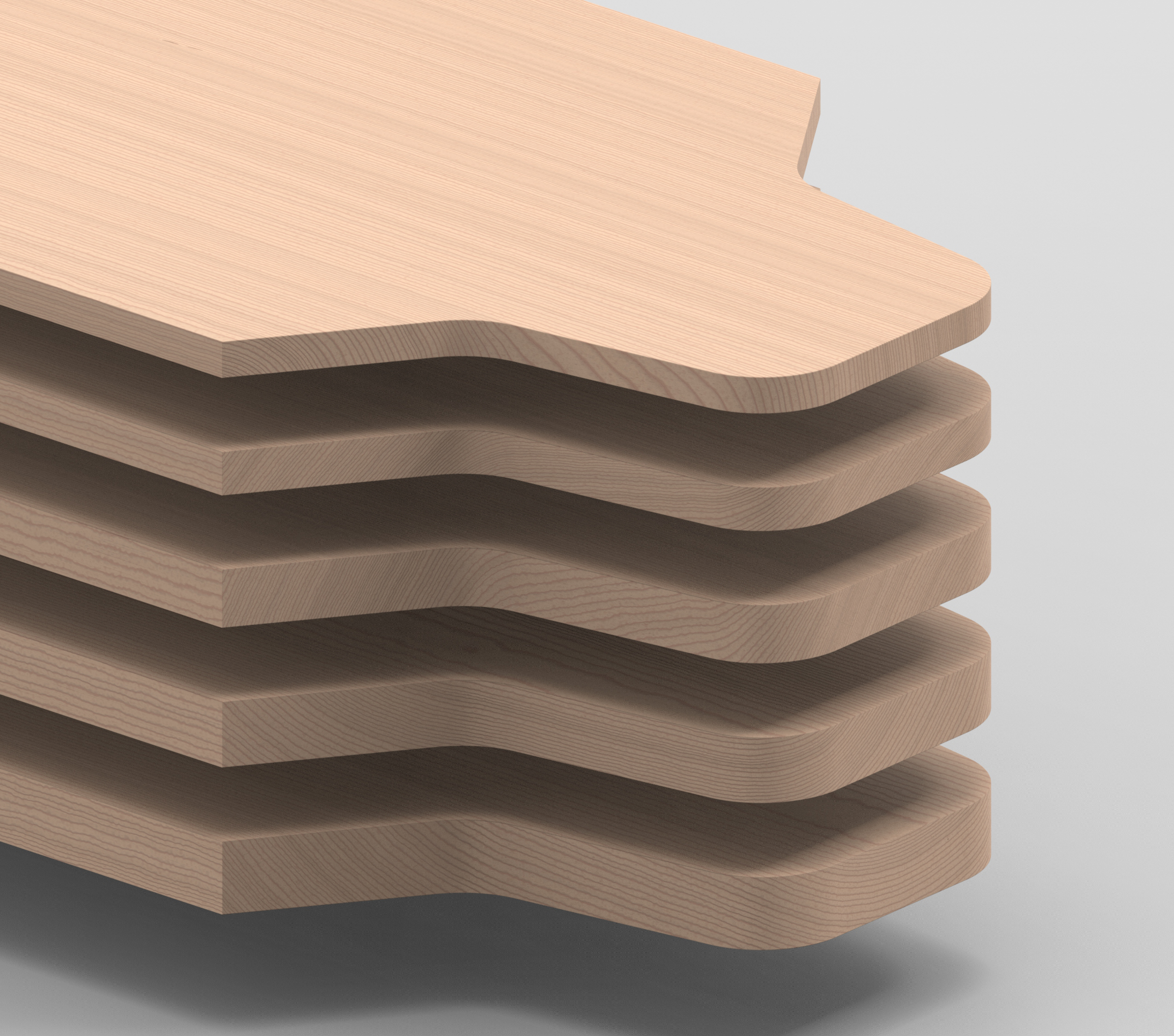
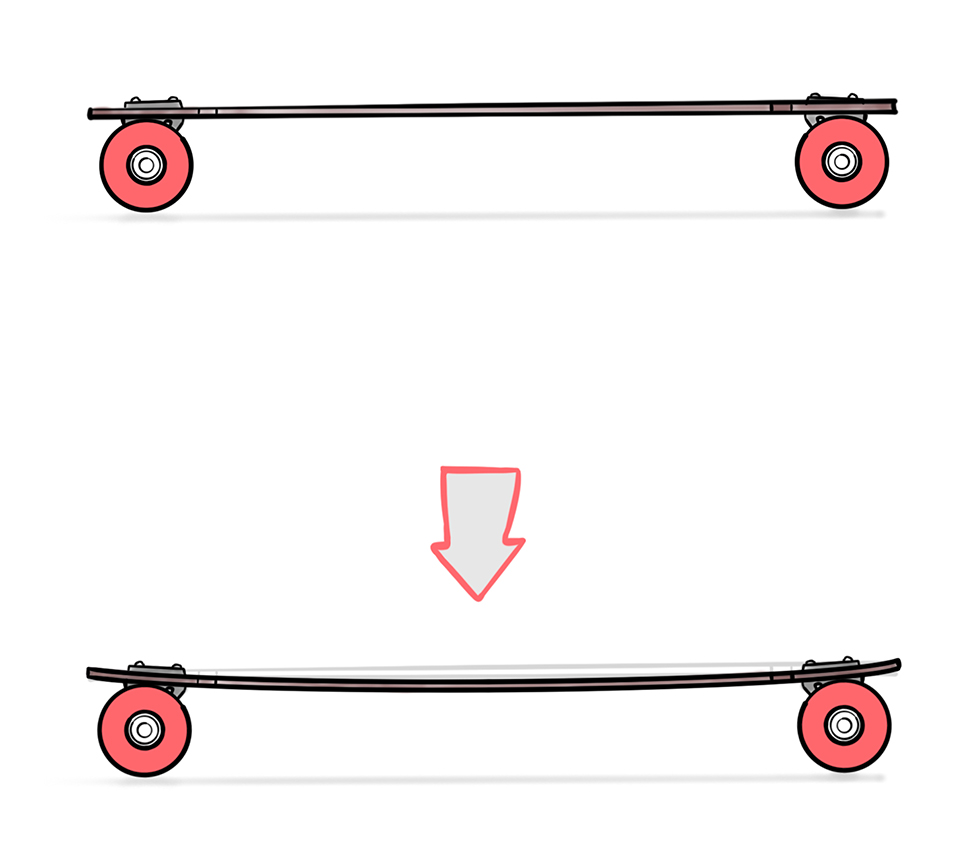
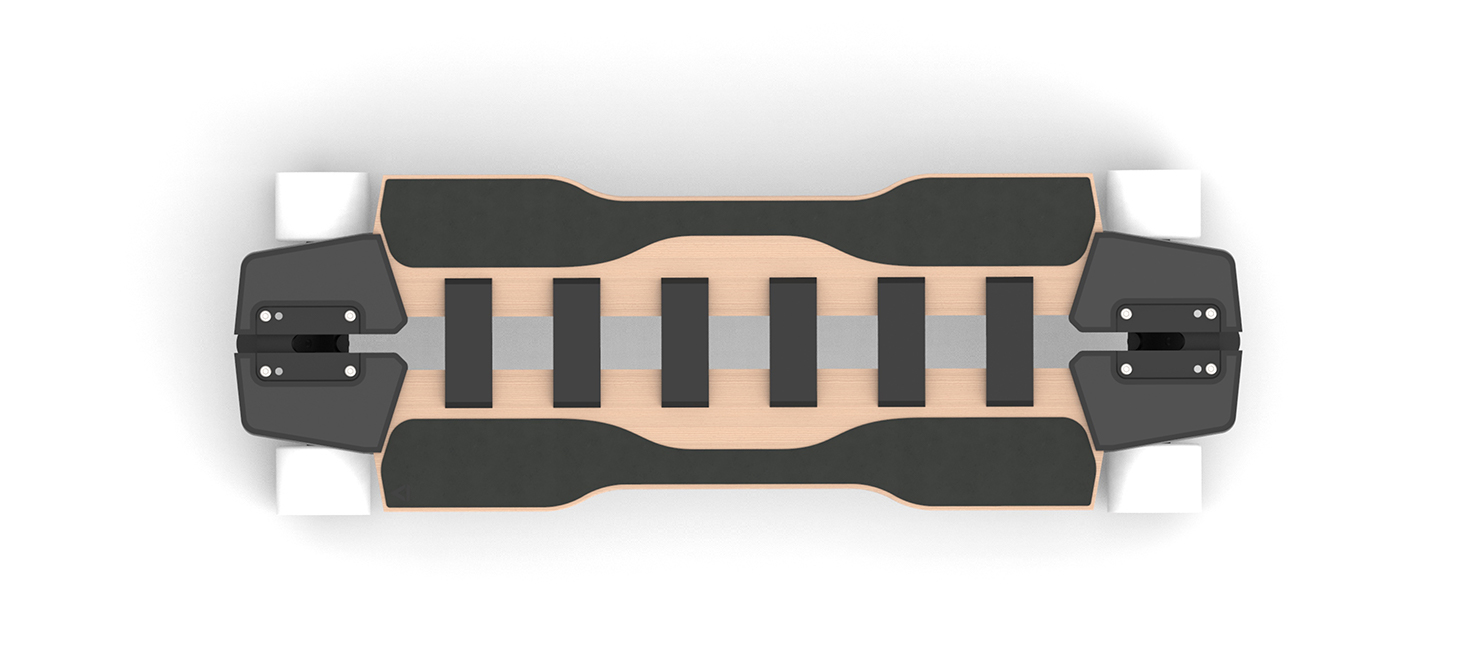
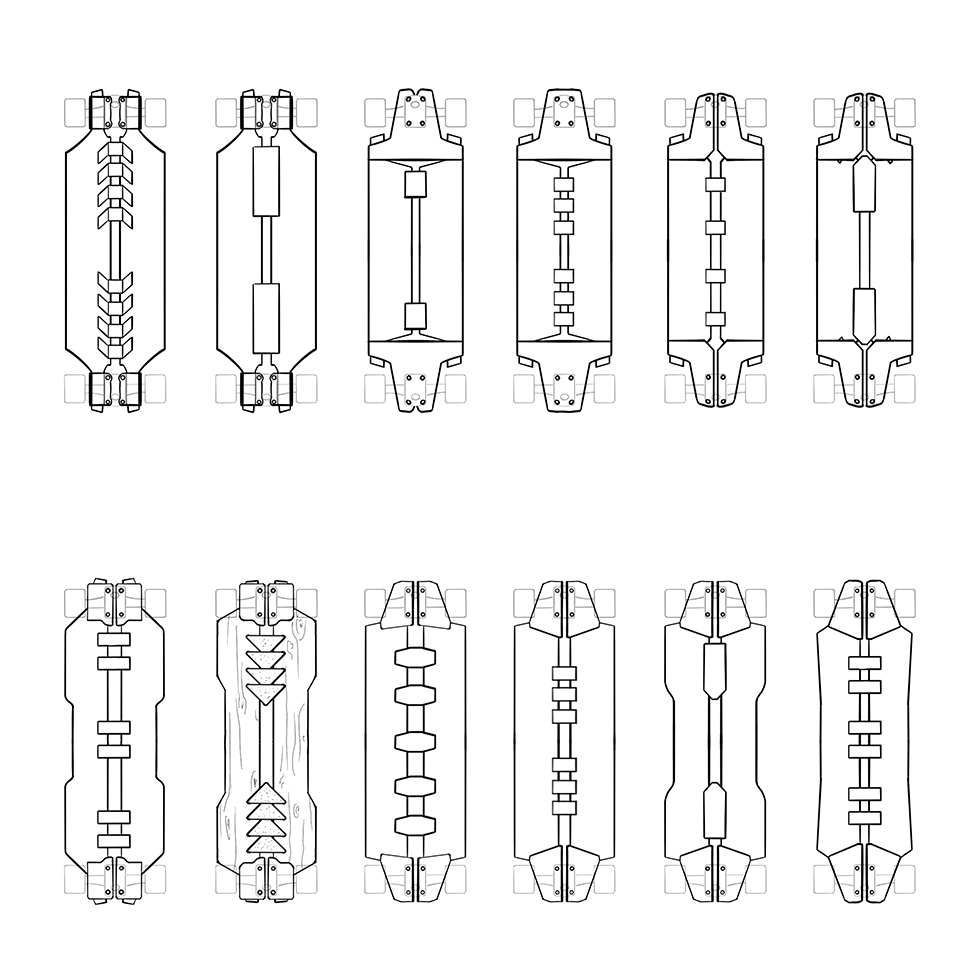
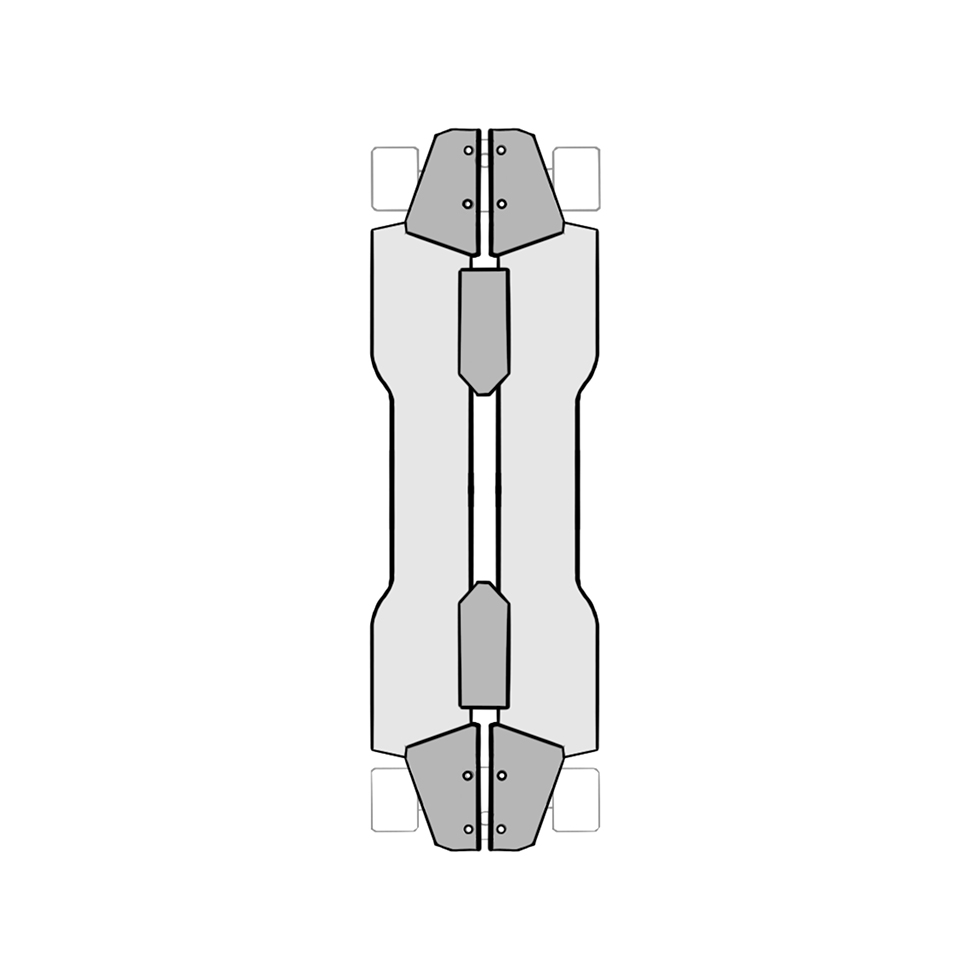
Board Three - Splitboard
The most radical design of the bunch. One thing solid wood is not good at is being shaped. Now with plywood you can put in a press and have it retain its shape easily, so this design is an attempt to shape a solid wood longboard deck without the use of a press.
The solution was to mix 3D printed elements even more drastically than any previous design. This way the board can have two different halves at an angle upwards mimicking a convex shape. The convex shape makes the board easier to make turns on.
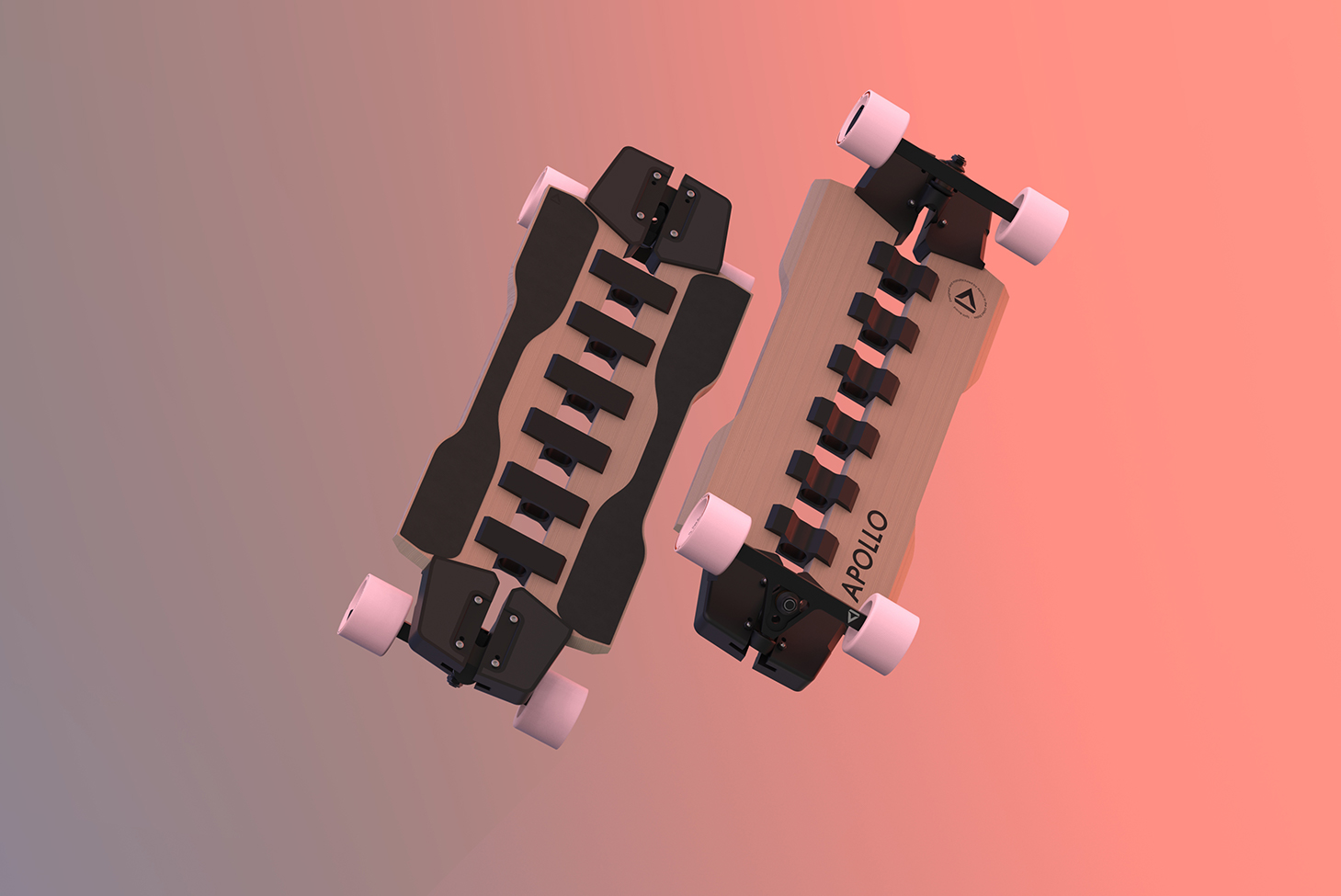
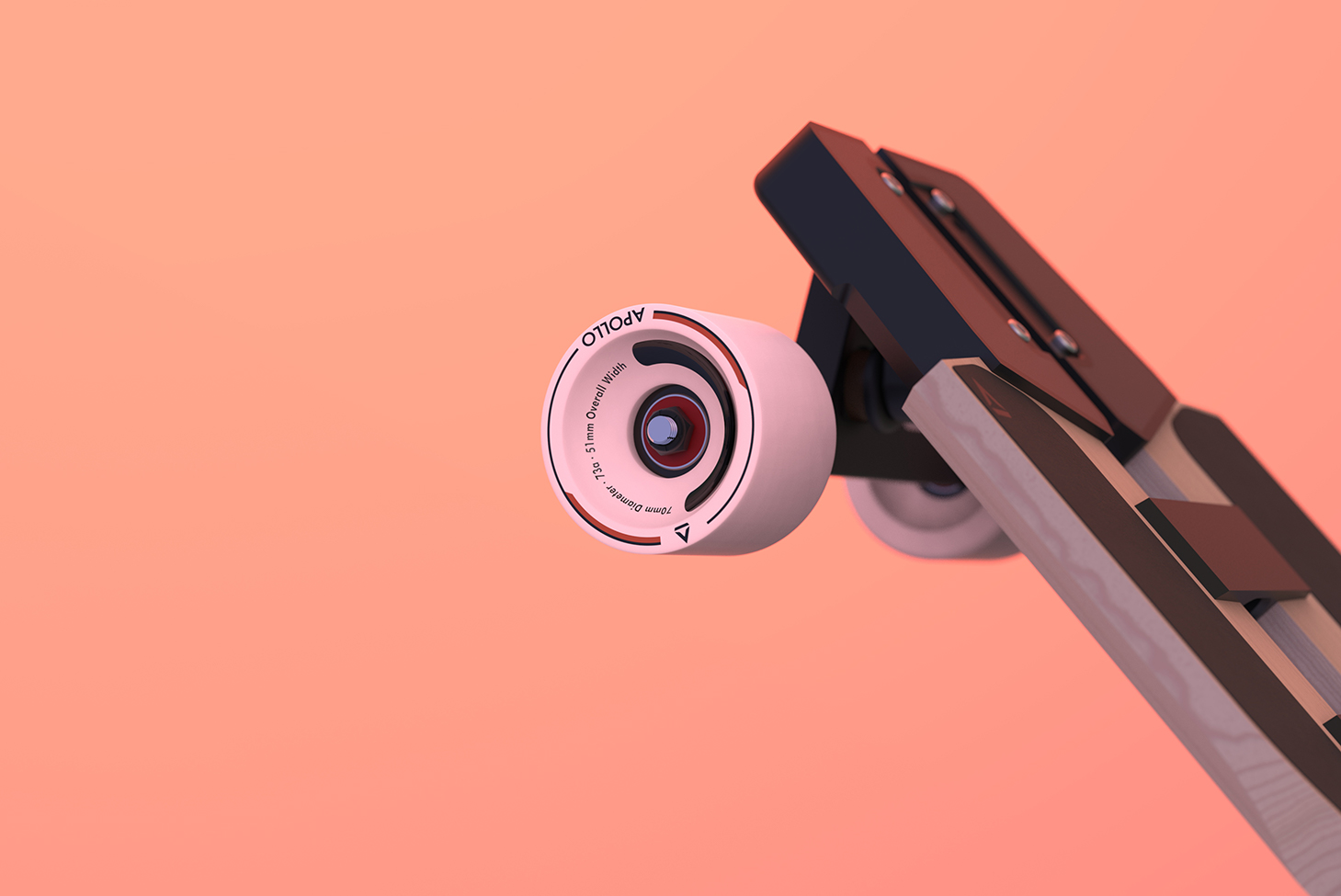
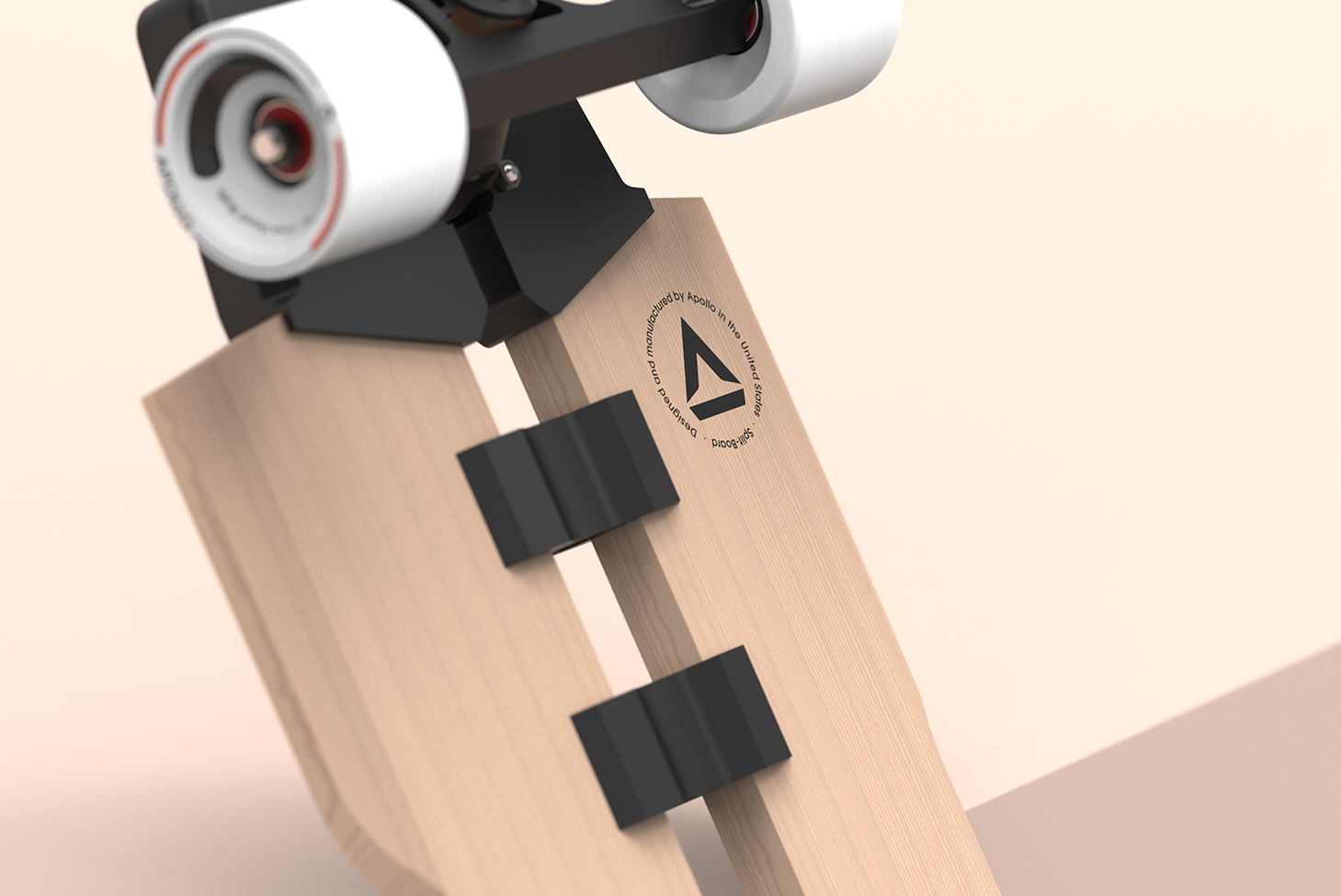